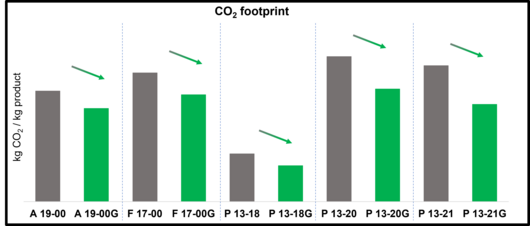
As part of the MOVE-TO-GREEN strategy, LEUNA-Harze GmbH commissioned the Institute for Energy and Environmental Research Heidelberg (Ifeu) to conduct a Life-Cycle Assessment (LCA) of selected epoxy resins and reactive diluents according to the LCA standards DIN EN ISO 14040/14044. The study included a detailed evaluation of the life cycle of the epoxy resins and reactive diluents from the production of the raw materials used to the factory gate of LEUNA-Harze GmbH (cradle-to-gate approach).
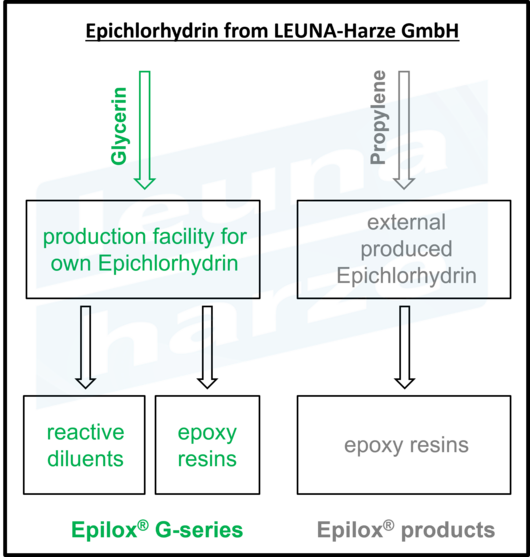
Propylen as starting material
The conventional method for producing epichlorohydrin uses propylene as a starting material, which is derived from fossil resources (petroleum). This multi-step process is initiated by the allylic chlorination of propylene. The subsequent reaction of the resulting allyl chloride with hypochlorous acid results in an aqueous reaction mixture of 1,3-dichloropropan-2-ol and 2,3-dichloropropan-1-ol. The epichlorohydrin is then obtained through a subsequent reaction with sodium hydroxide. Although this method is well-established on an industrial scale, its efficiency is limited, particularly due to the low chlorine atom economy.
Biobased-production from Glycerin
In the bio-based production of epichlorohydrin, glycerin is used as the starting material. In this two-step process, the glycerin used is first reacted with hydrochloric acid to produce a mixture of 1,3-dichloropropan-2-ol and 2,3-dichloropropan-1-ol. This is then followed by a reaction with sodium hydroxide to produce epichlorohydrin. This method offers a sustainable alternative to propylene-based production and results in less chlorinated waste per equivalent starting material.
The Epilox® products of LEUNA-Harze GmbH are produced using externally-sourced, propylene-based epichlorohydrin. Furthermore, at their own facility, they produce epichlorohydrin based on glycerin. This is subsequently converted, through a reaction with a specific alcohol, into products of the Epilox® G-series which have a bio-based carbon content.
In addition, the bio-based glycerin used by LEUNA-Harze GmbH is obtained as a byproduct of biodiesel production, primarily using waste of cooking fats as raw materials. The integrated implementation of the epichlorohydrin facility with the upstream chlorine-alkali electrolysis and hydrochloric acid synthesis at the LEUNA-Harze GmbH site not only enables the production of bio-based epoxy resins and reactive diluents but also the production of the necessary raw materials such as chlorine, hydrogen, hydrochloric acid, and sodium hydroxide.
Using in-house produced, bio-based epichlorohydrin for the production of epoxy resins and reactive diluents consistently results in a reduction of greenhouse gas emissions during the manufacturing process.
Moreover, there's also a comparatively low CO2 emission during the production of conventionally manufactured Epilox® products. This can be attributed mainly to the construction of new, modern facilities and the continuous optimization of processes and technologies.
Use of Renewable Energy in Production
A further reduction in CO2 emissions can be achieved, among other things, by using renewable energy. Plans to switch entirely to renewable energy sources in the production processes of LEUNA-Harze GmbH are set to be realized by 2035 and implemented in the manufacturing of epichlorohydrin, epoxy resins, and reactive diluents. The utilization of wind and solar energy will be particularly emphasized in this transition.